Greg Pendura, President, CEO and Chairman, and Don Weatherbee, CFO of Mineworx Technologies Ltd. Discuss their Unique Extraction of Palladium and Platinum from Diesel Catalytic Converters
|
By Dr. Allen Alper, PhD Economic Geology and Petrology, Columbia University, NYC, USA
on 11/5/2021
We spoke with Greg Pendura, President, CEO and Chairman, and Don Weatherbee, CFO of Mineworx Technologies Ltd., (TSXV: MWX, OTCQB: MWXRF, FSE: YRS, WKN: A2DSW3). Mineworx, in conjunction with its US based partner, Davis Recycling, is moving to unlock the massive opportunity of the extraction of palladium and platinum from diesel catalytic converters. The new proprietary processing technology, developed by Mineworx, presents a very efficient, economical, and environmentally friendly alternative, superior to smelting, which is currently the dominate method of recovery of palladium and platinum from catalytic converters. Diesel catalytic converters are a serious and growing problem, because smelters, worldwide, are beginning to reject batches that contain diesel catalysts, due to environmental hazards and processing issues they create. Mineworx’s technology will provide a commercially viable solution to process millions of diesel units that will be pouring into recyclers, over the next decade. The first commercial extraction facility will be built in Tennessee, USA, and it is expected to achieve over 90% metals recovery.
Dr. Allen Alper:
This is Dr. Allen Alper, Editor-in-Chief of Metals News, talking with Greg Pendura, President, CEO and Chairman of Mineworx Technologies and Don Weatherbee, CFO of Mineworx Technologies. Greg, I’ll start with you. Could you give our readers/investors an overview of your Company and also tell us a little bit about the technology and why it's important for recovering platinum and palladium in an environmentally correct way?
Greg Pendura:
On a basic overview, historically we were a junior mining company pursuing the traditional exploration and development model, but at the end of 2015 we found an opportunity to diversify into the mining technology business, by purchasing a private company that was developing environmentally friendly processing equipment. Over time, this base technology was adapted to allow for the recovery of precious metals from alternative sources and ultimately lead us into the recycling of platinum and pallidum from catalytic converters.
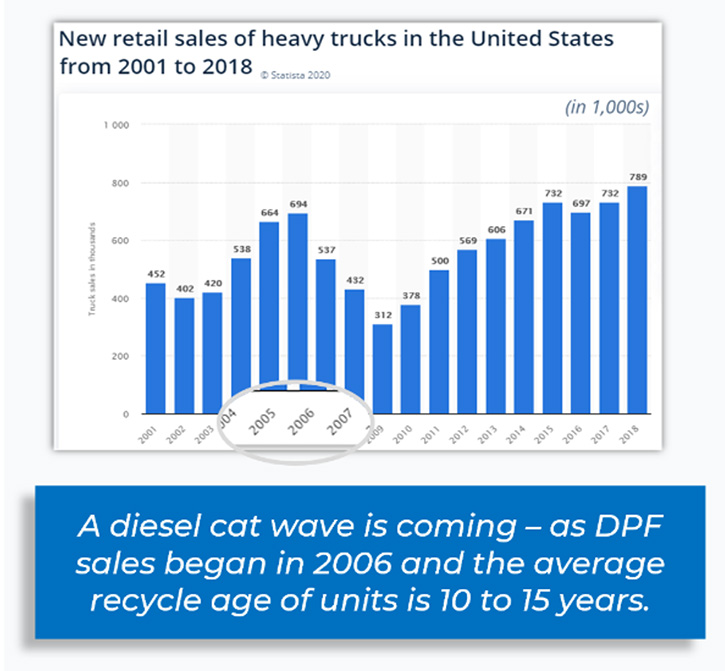
We have now focused on diesel catalytic converters, as marketplace dynamics are creating a niche opportunity. The current dominate method for recovery of platinum and palladium, from catalytic converters is smelters. Over the last few years, smelters have begun to refuse to process diesel catalytic converters because the honeycomb core that is comprised of silicon carbide interferes with the efficient operation of the smelting furnaces.
Currently, government regulations are increasing the requirement that diesel engines, across a broader spectrum, must have a catalytic converter. Now, in addition to the automotive and highway trucking sectors, Off-Road heavy construction vehicles, marine, and stationary industrial applications now also require a catalytic converter; effectively, anything containing a diesel engine has a catalytic converter associated with it. With limited smelter capacity, the increasing supply will have no place to go except landfills.
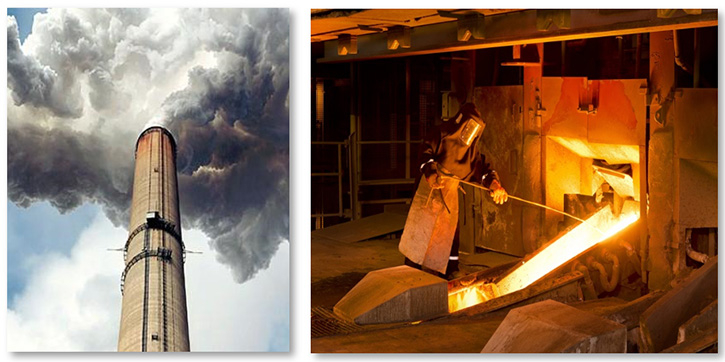
Mineworx is positioning itself to both divert precious metals from ending up in landfills, thus reducing the quantities that need to be mined by traditional methods and to work towards the reduction of the quantities, recovered by the smelting process, which also have issues on the environmental side. We have an environmentally friendly solution, that once commercial, will be able to recover a significant amount of platinum and palladium on a cost-effective basis.
That's the path we're taking. We have now relocated our pilot plant from Vancouver to Tennessee, where our partner, Davis Recycling Inc, is based. In Tennessee, we'll be commencing the process optimization stage of our testing plan, which is expected to provide the data needed to move to a commercial scale plant.
Dr. Allen Alper:
Oh, that sounds excellent. Could you tell us a bit about the process?
Greg Pendura:
The process itself is a leaching process, within a chemical solution. There are two processes, when you look at recycling catalytic converters. One is the preparation of the catalytic converter when it comes into a recycler’s facility. All large recyclers cut out the catalytic converter’s inner material, which is like a honeycomb that is plated with platinum and palladium. This removal of the honeycomb is also known as decanning.
The honeycomb is then ground and separated by various methods, where you eventually end up with a very fine powder material, which contains the platinum and the palladium. Historically, this powder was sent directly to a smelter, where the smelter would process it, in their furnaces, which would extract the precious metals. Our process replaces the smelter. The powder is still prepared the same way, but the powder will go into our leaching process, where the platinum and the palladium are extracted into solution and then recovered from that, back into solid form. I'll let Don speak to that, in a little more detail.
Dr. Allen Alper:
Sounds good, Don.
Don Weatherbee:
Our technology is really a four-step process. It's getting the precious metals into solution, which we do through the chemical leaching process. Then we recover the metals from the solution. We do that using traditional methods, like electrowinning. After the electrowinning, we sell the concentrate produced to a refinery who upgrades our product for the general marketplace. To be cost effective we need to recycle our chemistry, this recycling creates a closed loop system.
Dr. Allen Alper:
Well, it sounds excellent, and being a closed loop system, there are no chemicals going into the drain. Is that correct?
Don Weatherbee:
That's correct.
Dr. Allen Alper:
That sounds very, very good!
Greg Pendura:
It's basically an inert material, when we've completed the process. We're looking at ways to use the tailings, for example, in the cement industry, where all of the tailings can be used in a beneficial manner. Not just as a filler, but actually as an enhancement to the product as well.
Dr. Allen Alper:
Oh, that sounds great. Greg, could you tell us a little bit about your partner, Davis Recycling, and the role they're playing?
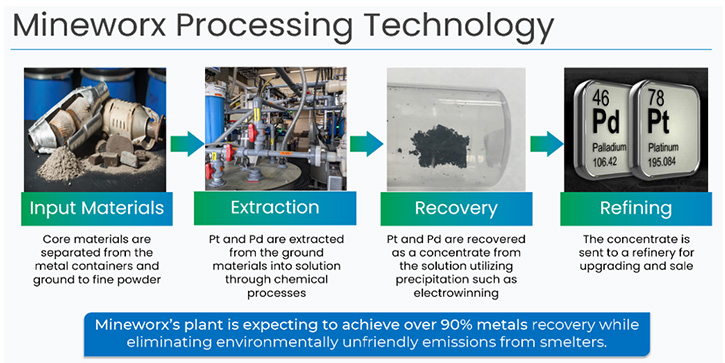
Davis Recycling is a large recycler, based out of Tennessee. They've been in the business for about 25 years. They are considered one of the larger recyclers, and they have a large facility in Johnson City, Tennessee, where they prepare the catalytic converter, into the dry powder format. Up until now, they have only been able to send it to smelters for processing.
In the past, the large recyclers, were able to mix a small portion of a container load of gas catalytic converters, with diesel catalytic converters and the smelters would accept that. More and more, as of late, smelters are refusing to allow that practice and are imposing significant penalties or outright refusing the entire container. We're getting to the point where diesel catalytic converters are going to be stockpiled or put into landfills. There are only a few smaller offshore smelters that will process diesel and they are operating at maximum capacity.
But the major reason we wanted to get involved with Davis Recycling, was simply because of their expertise in supply chain management. They have that whole part of the business well covered. They are very professional, all the way from their sales network to distribution, to having an up to the minute analysis of upgrades, pricing, and quality control. That whole material handling aspect of this business is crucial. Without expertise in that area, most companies, who would try to enter this space, would not survive. It’s a very complicated, complex endeavor and we've been very fortunate to align ourselves with Davis Recycling, because we feel that the major hurdle to this business is overcome by that partnership. Together we have created PGM Renewal LLC. as the commercial vehicle to move the business plan forward.
Dr. Allen Alper:
That sounds excellent! It's great to have such a strong partner and it sounds like you both complement each other, so that's excellent. Greg and Don, could you tell our readers/investors about your background and also a little bit about your Team?
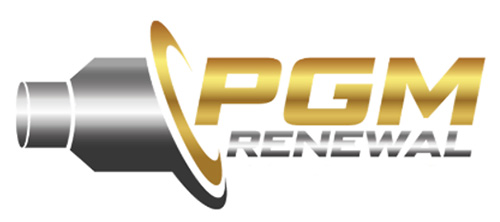
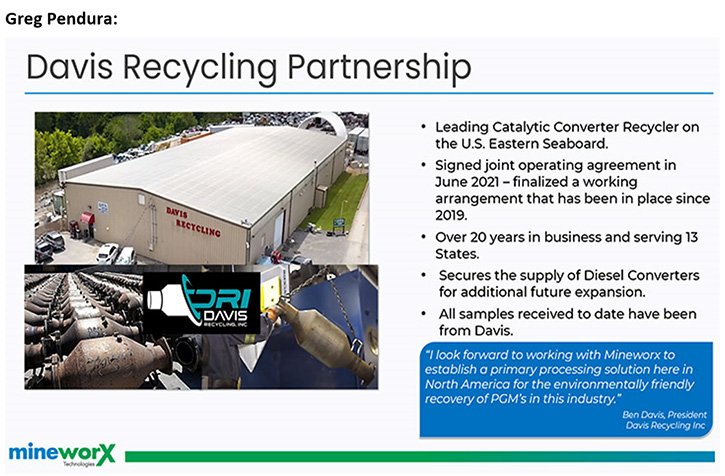
Don has the expertise on the mining side as well as finance, he's our CFO, I'll let him speak to that. I've been involved in the public markets for 25 to 30 years, in various public companies, which I've started and taken to more senior Boards, such as progressing from the TSX Venture to the TSX. My background is really on the Team building side. I've been involved in financing a lot of these companies, but really, I'm a Team builder. I like to find the key people that we need, such as Don, and build a Team around them.
Don's a very valuable member to our Team. We have a very strong Technical Team, led by Fabricio Maia, both in Vancouver and in Tennessee. We have a varied compliment of engineers, from chemical engineers to processing engineers. We have a full-sized lab in Vancouver, where we do a lot of our R&D and testing. We have a large fabrication shop in Vancouver. A lot of our background has been in fabrication, design, and installation of plants, in which we have a lot of expertise. We have different skill sets, within our organization, which complements what we're doing here on the catalytic converter side.
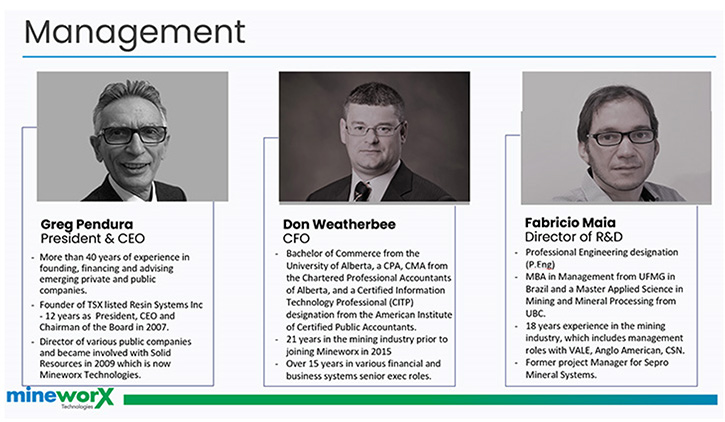
Dr. Allen Alper:
That sounds excellent. Don, do you want to add more information on your background?
Don Weatherbee:
I joined Mineworx in 2015. Prior to that, I'd spent just over 20 years, in a few different mining applications, in western Canada. I have a lot of experience in heavy equipment and utilization and operational baselines, with a finance lens to it. I am an accountant by training and have a strong operational bent to my focus.
Dr. Allen Alper:
That sounds excellent. I wonder if Don could talk about your share and capital structure.
Don Weatherbee:
We are traded on the TSX Venture and OTCQB in the U.S. We have just over 336 million shares outstanding, at this point in time. We have been trading at around the 10-cent mark lately. We’re well capitalized at this point. We did a large financing, at the beginning of 2021, which was well received and oversubscribed. In addition, we also have next to no debt on the balance sheet.
Dr. Allen Alper:
All right! Sounds very good! Greg and Don, could you tell our readers/investors the primary reasons they should consider investing in Mineworx Technology?
Greg Pendura:
I can mention a few key reasons and Don can probably add to it. We have a Clean Tech Technology, for the recovery of platinum and palladium, from diesel catalytic converters. Just on the environmental side, we will play a key role, I don't want to go into bad mouthing smelters because they have enough negative feedback, within the environmental landscape. But to have the ability to be able to recover precious metals in North America, both Canada and the United States, with an environmentally sound process, is extremely positive.
Everything has to be sent offshore to do any kind of processing of that particular type of material. So, what we will have to offer will be well received. Half of the platinum, which is produced annually, is used-up in catalytic converters. That's a large, large statistic. If you just think about 50% of all the platinum, produced every single year, going towards catalytic converters, you see the magnitude, or the scope, of the usage of precious metals in catalytic converters.
Also, only about a third of the catalytic converters are recycled presently. The remainder end up in landfills, which is a horrible waste. We're looking forward to being able to make a dent in what goes into landfills. But probably the biggest factor is that, if you can recover a lot of your platinum and palladium, you're reducing the mining side for platinum and palladium. The more you can reduce that, there's a tremendous number of environmental benefits, associated with that as well. There are a couple of factors here, which are connected, which are positive on the environmental side and on the investment side. We're quite undervalued for what we have and for where we're going to go. I see that as potentially a very strong opportunity for any investor, who gets involved at these levels
Dr. Allen Alper:
Sounds very good, Don! Do you have anything to add?
Don Weatherbee:
Well, Greg covered it quite extensively there. In simplistic terms, we're a great play for precious metals, without having to own a mining stock. We take out a little bit of the complexity in understanding the life of the mining stock, but you still have the exposure to precious metals, in an environmentally friendly manner.
Dr. Allen Alper:
Oh, that sounds very good! Do either of you have anything to add?
Greg Pendura:
I think it's pretty well covered. We are just about to enter our process optimization testing phase. Once that has been successfully completed, that will be the blueprint to complete our engineering and design for our commercial plant, which is expected to have a throughput of 10 tons per day. Once we tell the world we're building that plant and going down that path, there's going to be a lot of press and exposure for us and we're going to be well on our way.
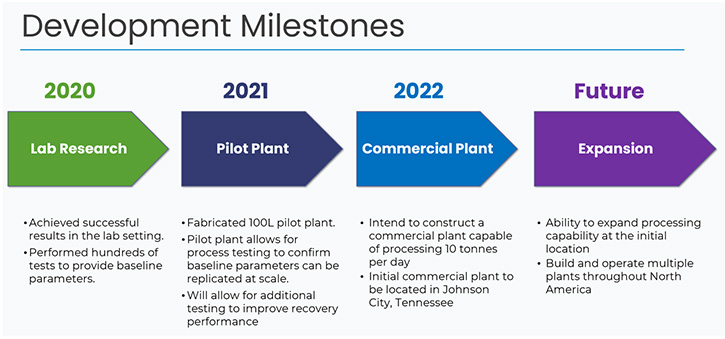
Dr. Allen Alper:
I am very impressed, with what you are doing! It sounds like you have an amazing opportunity to make a very important contribution, for both the United States and Canada, in an extremely critical area! We’ll publish your press releases as they come out, so our readers/investors can follow your progress.
https://www.mineworx.net/
Greg Pendura
780-800-0726
greg@mineworx.net
|
|