Ucore Rare Metals Inc. (TSXV: UCU) (OTCQX: UURAF): Developing Rare and Critical Metals Resources, Extraction, Beneficiation and Separation Technologies, with Potential for Near-term Production; Pat Ryan, Chairman and CEO, and Mike Schrider, VP and COO Interviewed (Part 1)
|
By Dr. Allen Alper, PhD Economic Geology and Petrology, Columbia University, NYC, USA
on 8/5/2021
We spoke with Pat Ryan, Chairman and CEO, and also Mike Schrider, VP and COO of Ucore Rare Metals Inc. (TSXV: UCU) (OTCQX: UURAF). Ucore is focused on rare and critical metals resources, extraction, beneficiation and separation technologies, with potential for production, growth, and scalability. The Company's goal is disrupting the People’s Republic of China’s dominance of the US REE supply chain, through the development of a heavy rare earth processing facility – the Alaska Strategic Metals Complex (the “Alaska SMC”) in Southeast Alaska and the long-term development of Ucore’s heavy rare earth element mineral resource property, located at Bokan Mountain, on Prince of Wales Island, Alaska. In May of 2020, Ucore acquired Innovation Metals Corporation that has developed a patent-pending proprietary, environmentally sound, and 21st-century critical metal separation technology platform, called RapidSX, to be implemented at the Alaska SMC
Ucore Rare Metals Inc
Dr. Allen Alper: This is Dr. Allen Alper, Editor-in-Chief of Metals News, talking with Pat Ryan, Chairman and CEO, and Mike Schrider, VP and COO of Ucore Rare Metals, Inc. Maybe, Pat, you could start off. What is the vision of your Company? Give us an overview of the Company, and what differentiates your Company from others?
Pat Ryan: Certainly. Ucore’s vision is to supply critical materials, within the rare earth sector, founded on a 21st-century North American technology, strategically breaking the dominance that China has had on that market and eventually, in other critical metal markets, like battery metals. There's a lot of talk these days about who controls different sections of these critical supply chains - China controls about 85% of the global rare earth oxide production and about 90% of the rare earth component production, like permanent magnets. These components fit in the rapidly growing world of the electrification of vehicles; primarily in the permanent magnets, used in components like windows, locks, and other features, but most importantly in the drivetrain motors. 90% of electric vehicle drivetrain motors are permanent magnet synchronous motors, containing rare earth metals. These are used by Volkswagen, Toyota, General Motors, and many others. Electric vehicle [EV] market penetration will grow, from a current small percentage of total vehicles produced, to 1/3 of the total annual vehicle production, by the end of the decade, or approximately 30 million of the currently 90 million global vehicles produced each year, COVID aside.
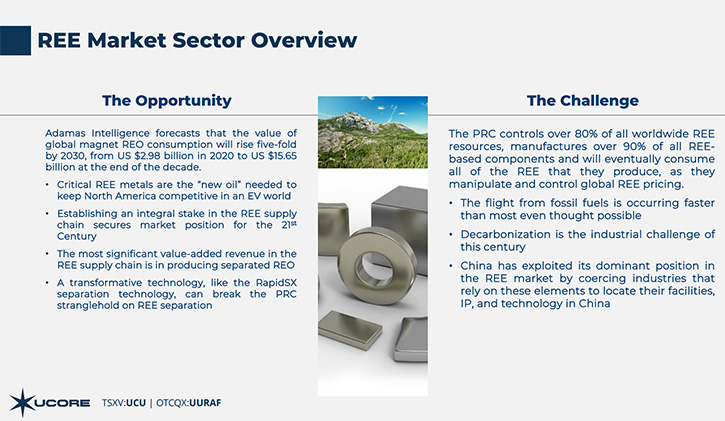
We need to break that rare earth dominance from China. Ucore is working every day to be the technology and domestic resource company, focused on the critical aspects of the Western rare earth supply chain that China now controls. The supply chain has an ‘upstream’, which includes rare earth ore and rare earth mineral concentrate. That's where your mines and your mills are. When you get to that center section or the mid-market of the supply chain, that's where the separation of oxides happens. Separating mixed rare earth concentrate to high purity individual metal oxides is a time-consuming and expensive process. That is the product, however, that is required by metal and alloy makers and 85% of that process is currently happening in China. There is really only one Western separation facility - that Lynas operates in Malaysia. Then downstream, of course, we have the metals, the alloys, and the permanent magnet manufacturing, which are finally customized for individual rare-earth-containing components.
That center section of the rare earth supply chain is what the US and North America must address to regain control, and the way to do that is with technology. Currently in China, they're using solvent extraction [SX] technology – the current standard for rare earth processing around the world. It's very cumbersome, takes up a lot of space, and to set up something like that in North America would probably not be the competitive way to move forward. So, in May of 2020, after a global search and a comprehensive due diligence evaluation, Ucore acquired a company called Innovation Metals Corporation [IMC]. IMC developed a technology, over the last 10 years, known as RapidSX™. RapidSX™ technology requires a much smaller footprint than what you would have in a typical SX plant. However, it's based on the same chemistry of solvent extraction, but the processing happens much quicker. The OPEX is currently on par with Chinese operators and probably at 10% less by the time we get our commercialization project completed at our Kingston, Ontario facility, which is targeted for the end of this year. So this all fits in, breaking that China stranglehold on supply, and again, it's technology-based.
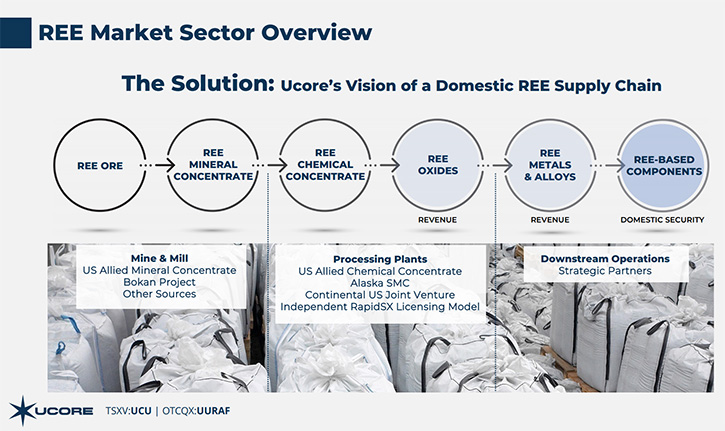
We’ll then look to transition to other critical metals. Battery metals that are currently in high demand, due to the EV revolution and the renewable energy industry’s increasing demand for lithium-ion battery storage. Again, technology is the key that will get it done.
Of course, our supply chain position is augmented by our longer-term resource project at Bokan Mountain in Alaska. Bokan-Dotson Ridge is a heavy rare earth resource, in which we’ve invested over C $35 million to date, and that we are continuing to invest in, to move the project towards production. It's the highest grade, heavy rare earth element resource on U.S. soil, disclosed under NI 43-101 standards. And so that too is very exciting.
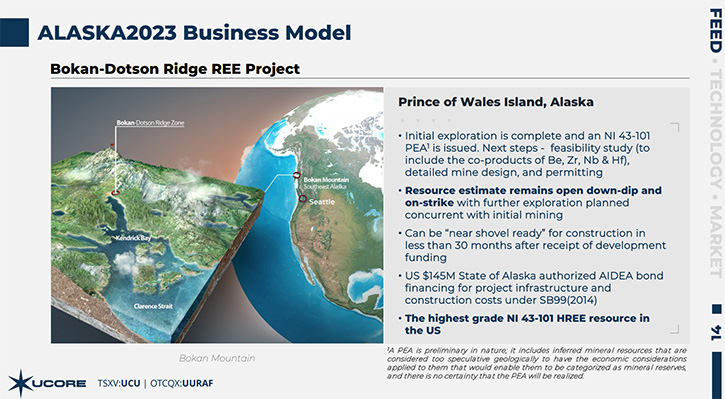
At the end of the day, with the RapdidSX™ technology, Ucore can deliver environmentally sound and economically competitive rare earth oxides to the market, through self-use, through partner-use, and also through IMC’s strategic licensing opportunities. The self-use is by virtue of the Alaska Strategic Metals Complex [SMC]. It’ll be the first worldwide commercial deployment of the RapidSX™ technology, bringing rare earth separation of oxides to U.S. soil. I'll let Mike speak to this, a little more definitively. So, it's a three-prong opportunity, long-term, with the Bokan project, short-term in Alaska SMC, and all of it is driven by technology. It's a technology company transition, and we're starting with rare earth metals, the most complex to separate, and we'll move from there to other critical metals.
Dr. Allen Alper: Oh, it sounds excellent! Sounds like Ucore is playing a key role in electrification of the world and EV batteries.
Pat Ryan: Yeah, very much so!
Dr. Allen Alper: Maybe Mike could tell us a little bit more about the RapidSX technology. My understanding is, not only is it going to be used for yourself, but it sounds like you might license it, or apply it, or develop work with partners on it. Maybe you could elaborate on some of that.
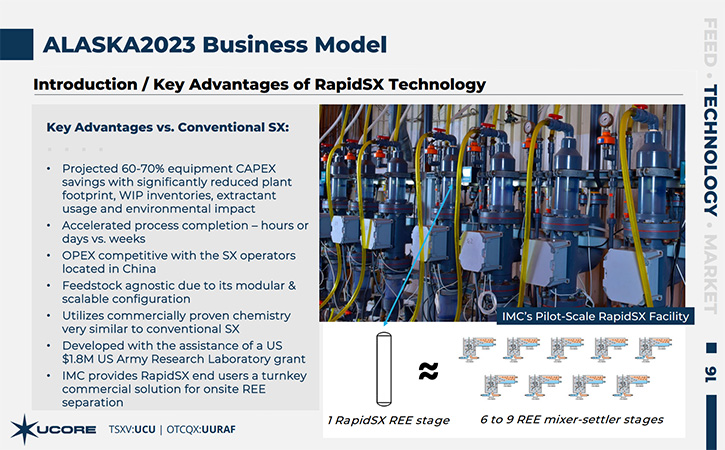
Mike: Certainly. RapidSX technology has numerous key advantages over conventional SX. In addition to the competitive OPEX that Pat mentioned, the projected CAPEX savings versus a traditional SX plant is about 60 to 70% on the equipment and then, of course, there's a corresponding reduction in the plant footprint, the work in progress inventory, the extractant usage, and the environmental impact – which is lessened because we're utilizing significantly fewer organic solvents. Regarding the processing time, we're talking hours or days versus weeks, due to the increased reaction kinetics and the decrease in circuit complexity. It's virtually feedstock agnostic, due to its modular and scalable configuration, which can be readily adapted to a change in feedstock supply. And it utilizes commercially proven chemistry, which is virtually identical to that used in SX technology. So, we're not re-inventing the wheel, with regard to the chemistry. We're just applying it in a different manner and taking advantage of the application process through physics.
The origins of Rapid SX were initially developed at the tail end of a US $1.8 million U.S. Army research laboratory grant and then further enhanced through pilot-scale by IMC, prior to the acquisition by Ucore. As Pat mentioned, there is a commercialization effort underway, right now, at our Kingston, Ontario, facility where IMC is optimizing the Rapid SX technology for commercial deployment and is developing standardized turnkey engineering and equipment packages, for end users. The idea is to have standardized modules, for self-use. As an example, at the Alaska SMC in Ketchikan, Alaska; for potential partner use in the continental US; and through IMC, to also license them as prospective strategic partners in the Western rare earth sector.
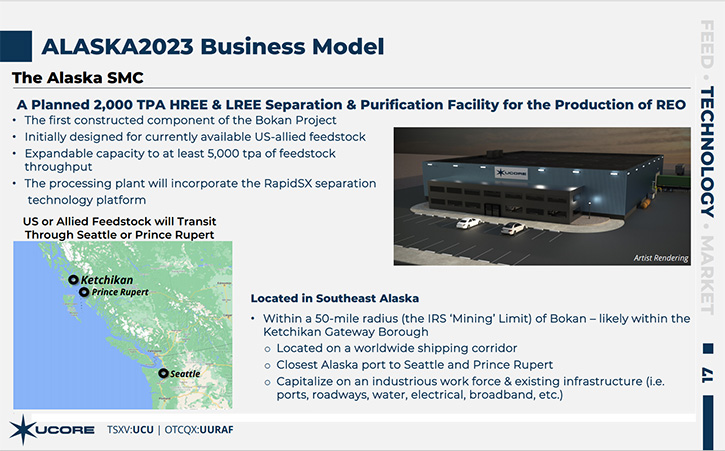
Dr. Allen Alper: Oh, that sounds exciting!
Pat Ryan: I think it's important to note, too, that with a conventional SX plant, when something goes wrong, like a power failure, or whatever knocks out the SX plant, to get it back into equilibrium, after restart, can often take days or weeks before you can start producing to specification again. With RapidSX, you can get back to equilibrium in hours and get back to generating revenue, much more quickly. This is especially important when thinking about work-in-progress inventories and the time, money and labor that is saved by virtually being able to batch process with RapidSX – a design goal that the IMC Team is working on.
Power supply, to huge SX operations like the original Molycorp at Mountain Pass in California, was extremely problematic. Their biggest issue was that the power would go down quite often and it often took weeks or a month to get it back up and running again. You can't run an operation that way. The time to equilibrium, with Rapid SX, is a huge advantage.
Dr. Allen Alper: Your process definitely has a competitive advantage of cost, size, and footprint, so that's excellent and environmentally much better. That's really great! My understanding is patents have been applied for, this technology.
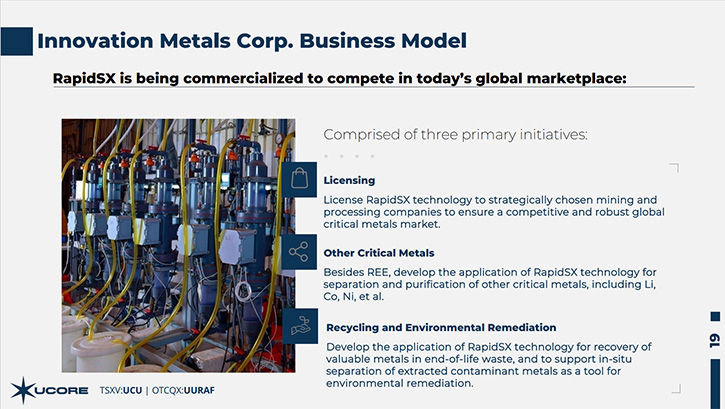
Pat Ryan: Yes, patents have been applied for, but our holistic intellectual property strategy is still evolving. Because we'll have a mixture of self-use and licensing, we want to make sure that we take the correct approach regarding patents vs. trade secrets. So, it's still under evaluation.
Dr. Allen Alper: I ran a rather large business of tungsten, tantalum, and more for Osram Sylvania, and there's always a choice, what you hold secret and what you publish and the ability of others to copy your work and get around it. So, I understand your predicament. Could you, Pat, tell our readers/investors your primary objectives for 2021 into 2022?
Pat Ryan: The primary objective is the commercialization of the technology. The technology is at the center of everything. The ability to separate the oxides and break free that middle market (as I defined it) that the Chinese now control. When you get control of that middle market, you control the supply chain. So far, China has done that effectively, including the acquisition of foreign sourced materials to China for their own manufacturing requirements. Take MP Materials, all of their concentrate is sent to China for processing. That's not an effective American solution. So, our first priority is to get this technology through to commercialization, and we're doing that right now. As mentioned, IMC is currently optimizing the process at the Kingston, Ontario, facility. Innovation Metals is working, in collaboration with Kingston Process Metallurgy [KPM], and the Science Team, led by Dr. Gareth Hatch, who has tremendous experience in this area. The Team also includes Dr. Kurt Forrester, a global expert in metallurgy and chemical engineering. They're accomplishing objectives and achieving milestones, every month, to get us to commercialization.
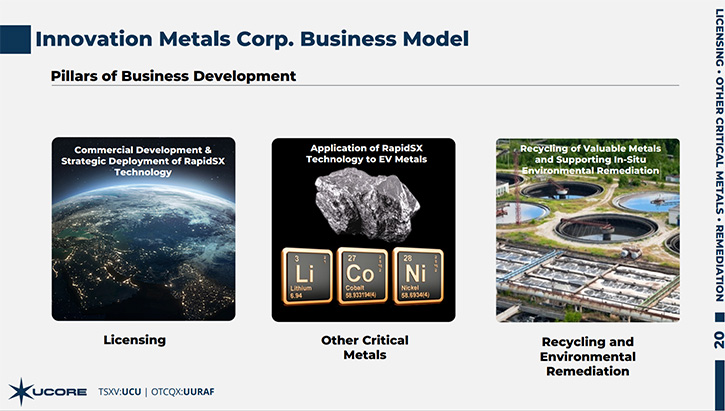
Concurrently, we have also just commissioned an Independent Evaluation of the RapidSX technology to be overseen by a third-party, independent hydro-metallurgist, to verify our technoeconomic processing data. This verification process will independently validate our capabilities, highlight our advantages and will demonstrate to our various stakeholders the effectiveness of RapidSX technology from an independent perspective. So, it won’t be just our science team proving out the technology, establishing our metrics and getting things done, but here's an independent voice that confirms the CAPEX savings, the OPEX savings, the accelerated reaction kinetics and the associated equilibrium recovery savings, are all on point. So that's certainly our first objective – to commercialize the technology while establishing an independent evaluation of its efficacy. Obviously, these checks and balances are imperative to both Ucore, our prospective partners, and investors.
A second objective is to continue to advance our initiatives with the Alaska SMC. Mike is spearheading the effort to develop this facility. Including the engineering construction plans that will incorporate the RapidSX technology, as well as to develop the state-of-the-art procedures and processes for everything that, comes before and after the RapidSX separation process. And along with IMC, identifying, testing and securing the US-allied feedstock sources that the plant will process. We're also working closely with AIDEA, that's the Alaska Industrial Development and Export Authority. AIDEA continues its long-term support of all aspects of Ucore’s development efforts, in Southeast Alaska, and we're anticipating that they, along with other prospective partners, will help with the initiation of the Alaska Strategic Metals Complex, in Ketchikan, Alaska. Hopefully, the first operating commercial rare earth separation plant on US soil - by 2023.
A third objective, which Mike can speak to, is some near-term work related to Bokan. If you don't continue to advance your most valuable asset, then what are you doing? We have designated funding that we have initiated for further mill flowsheet development and we have plans for a field program to continue to advance and upgrade the Bokan resource a little bit further. So, that too is important.
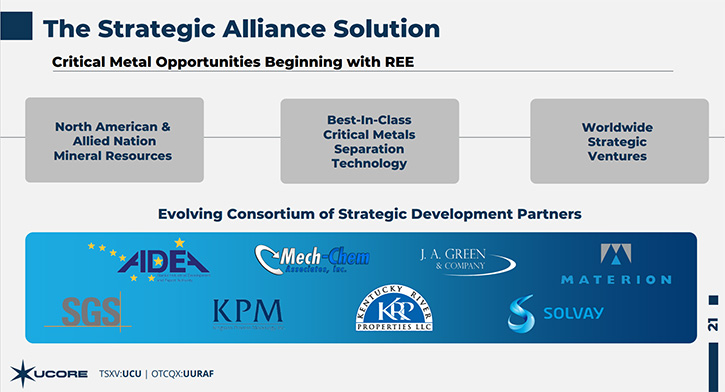
And finally, the other important thing that we're doing is establishing our downstream business connections. We're working with companies like Materion, a vertically integrated beryllium producer, with many parallels to the rare earth supply chain. We have an established relationship with them and are discussing various alternatives that might be possible in the downstream metal alloy making, where Ucore and IMC can benefit from their mine to metal beryllium experience. We also have other key industry players that have reached out to us from the EV automotive world, and they too are trying to consolidate the domestic rare earth supply chain; including risk aversion, ethical and secure sourcing requirements that go right back to the oxides, and quite frankly, right back to the mine.
So, as mentioned earlier, it's a three-prong opportunity that we're looking at. The technology, we have to prove it out and deploy it on commercial scale to capture the middle market. Upstream, we're continuing to work on developing Bokan as an ultimate secure source of domestic heavy rare earth supply. Downstream we have evolving relationships that we're working on to penetrate the end-user market, and all of it being supported with various government initiatives and our own strong capital. So, that's the position and a high-level overview of what we're up to at Ucore, in a very busy 2021.
https://ucore.com/
Patrick Ryan, P.Eng.
Chief Executive Officer
Chairman of the Board of Directors
Ucore Rare Metals Inc.
Mark MacDonald
Vice President, Investor Relations
Ucore Rare Metals Inc 902.482.5214
mark@ucore.com
|
|