Saltworks Developed and Commercialized Technology for Lithium Mining and Processing Companies, Interview with Ben Sparrow, CEO of Saltworks Technologies Incorporated
|
By Dr. Allen Alper, PhD Economic Geology and Petrology, Columbia University, NYC, USA
on 9/25/2018
We interviewed Ben Sparrow, CEO of Saltworks Technologies Incorporated, a Canadian industrial desalination and advanced water-treatment Company. Saltworks developed and commercialized a technology that can help lithium mining and processing companies extract lithium from brine more economically. We learned from Mr. Sparrow that they developed a chemical softening robot that is much more compact, much more precise, easier to use and automated, compared to standard reverse osmosis systems. At the membrane treatment step, Saltworks developed the ability to remove and manipulate ions in water selectively and they created special membranes that can selectively pull lithium away from calcium or magnesium. Saltworks also created membranes tolerant to oil and gas, where they can desalt oil and gas produced water. At the thermal treatment step, Saltworks built a more reliable evaporative crystallizer made out of fiberglass so it doesn't rust. It cleans itself, doesn't stick, and has a built-in solids management system. Saltworks has two factories in Canada, about 40 patents, and its shareholders include British Petroleum, ConocoPhillips and Teck Resources.
SaltMaker Multi-Effect Evaporator Crystallizer
Dr. Allen Alper: This is Dr. Allen Alper, Editor-in-Chief of Metals News, interviewing Ben Sparrow, who's CEO of Saltworks Technologies Incorporated. Could you give our readers/investors an overview of your company, your focus and current activities?
Ben Sparrow: Saltworks is an industrial desalination and advanced water treatment company. We specifically focus on moving ions around and water treating complex brine, high fluidity brine, extracting value from them, so anything to do with the periodic table of elements in water beyond where conventional reverse osmosis operates.
We're based in Canada. We have two factories. We build both thermal systems that evaporate and we also build membrane pistons whether they be reverse osmosis or very special ion exchange membrane that we make ourselves, and that membrane ties in with lithium.
We have about 40 patents. Our shareholders include companies such as BP, British Petroleum, ConocoPhillips and a large mining company, Teck Resources. They all invested in our company because the technologies, on which we were working, have developed and commercialized and impact their ability to operate more economically as the world encounters harder to extract hydrocarbons, stricter water district centers, and then tying it back to mining and lithium. Really, lithium mining is water mining. So we've found that some of what we've been working on may be able to help some of the lithium producers.
Dr. Allen Alper: Could you tell us, our readers/investors, more about your technologies and the type of problems you’ve solved. I’ve interviewed many, many lithium companies, which are brine companies, all over the world. Could your technologies be used by the lithium miners and manufacturers to produce lithium carbonate, et cetera?
Ben Sparrow: The problems that we work on and the technologies that we employ, are focused on brine treatment. This is challenging salt water that you can't treat with normal, off the shelf, reverse osmosis systems. We attack it three ways. Most people do chemical treatment, membrane treatment, and then thermal treatment. What differentiates our technologies is that, on the chemical side, we've developed a chemical softening robot, so a chemical softening machine that's much more compact, much more precise, easier to use and automated.
People have been doing chemical softening for many, many decades, and they've been doing it essentially the same way for many, many decades. So we've just modernized chemical softening. What differentiates us, is our ability to remove and manipulate ions in water selectively. This is where it ties in with lithium. With these very special membranes that we've developed, we can extract monovalent ions and reject divalent ions with only like a 98% rejection rate.
We can pull chloride away from sulfate selectively. We can pull lithium away from calcium or magnesium selectively. That enables you to do all sorts of things, whether it be to refine a solution, or change the fundamental chemistry. With membranes tolerant to oil and gas, we can desalt oil and gas produced water, hence the investment of British Petroleum and others. Previously you would swell and damage the membrane, so we built this really robust, very special membrane and membrane system.
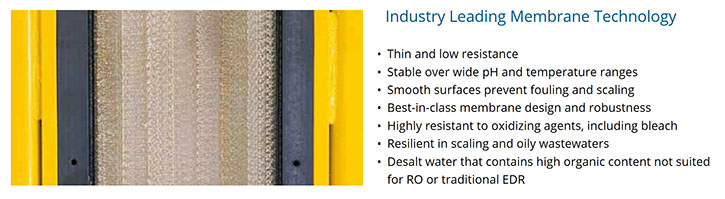
Then on the thermal side, anybody can boil water. People have been doing that for many centuries. We've been evaporating and crystallizing. We've looked under the hood of these various processes and the end users had a lot of challenges with them. We built a more reliable evaporative crystallizer, made out of fiberglass, so it doesn't rust. It self-cleans, it is non-stick, and it has a built-in solids management system. Both our customers and we view it as a simpler, better evaporative crystallizer.
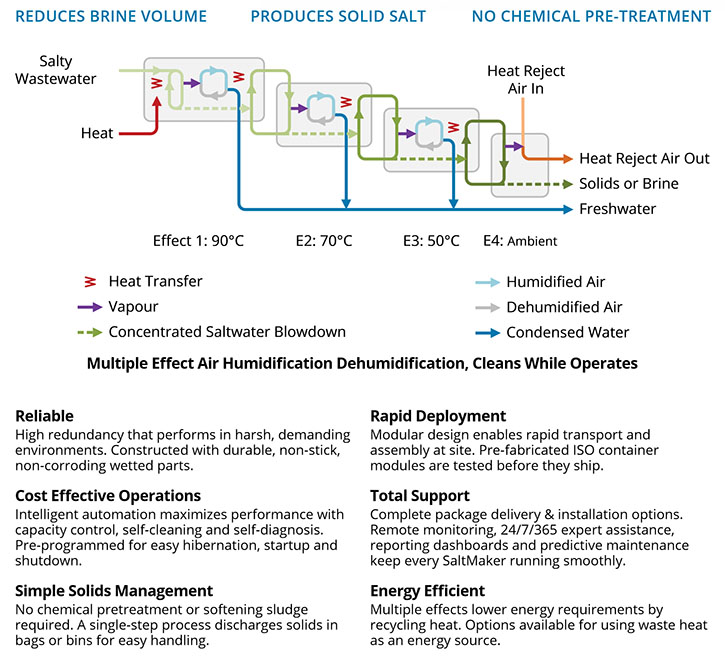
Ben Sparrow: When it comes to the lithium industry, we can split our work into two categories; advanced lithium extraction and conventional lithium extraction. There are applications for both. In the advanced lithium extraction, the ion exchange membrane that is monovalent selective is excellent.
Ben Sparrow: I'll explain the process. In the blue chamber, we're flowing a saline water source that may have lithium in it. In the red chamber, we're concentrating lithium chloride, or lithium sulfate. This is the video of the process. These lithium brines have a lot of hardness in them, calcium magnesium, hardness is really a pollutant to lithium production, and whenever you try to precipitate out the hardness, you end up co-precipitating some lithium, and so there's a yield loss.
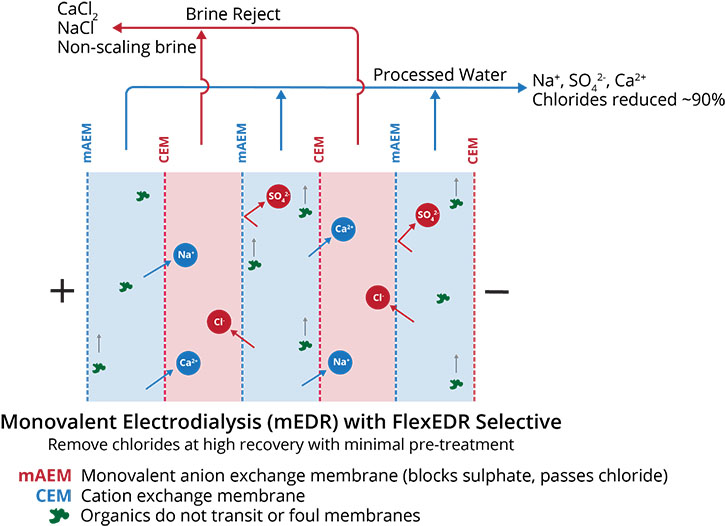
That's point one. The other thing is, as you probably know very well, people spend a lot of either energy, thermal energy, or land area in dry regions to build these ponds to evaporate water to concentrate lithium. Our electrodialysis reversal, using monovalent membrane, does two things at the exact same time. It purifies the lithium away from calcium magnesium, and it simultaneously concentrates. It concentrates electrochemically, and so we can achieve a concentration ratio of something like 10 times, which means your ponds could be 10 times smaller, and you wouldn't suffer lithium co-precipitation loss when you precipitate out calcium magnesium because of the electrochemical membrane separation process.
You have to spend money on electrical power to run the electrochemical process, so it is more electrically energy intensive, it's much more compact, however, and it doesn't require chemical input, so there's this trade off that needs to happen.
The second link includes specification sheets, and on the second page, you'll see this sort of yellow plate and frame membrane stack. These are modular stacks, about the size of a large refrigerator, and inside are the membranes. You pull the water through it, and you apply a charge to the outside, and out comes a much more highly concentrated lithium chloride solution with far less bivalent ions in it. It'll still have sodium in it, so it'll be lithium sodium chloride if that's present. This will purify and concentrate lithium at the same time.
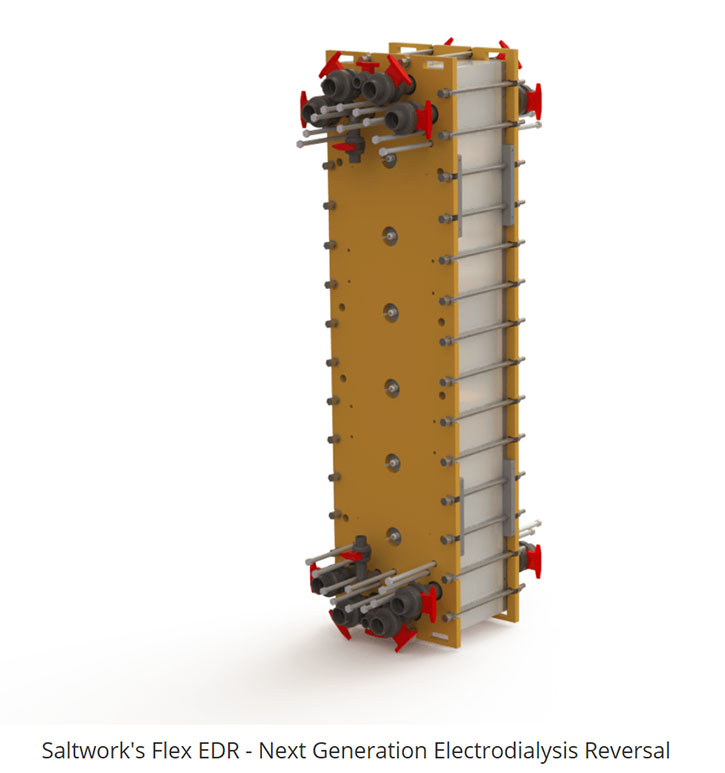 Figure 1 Saltworks Flex EDR - Next Generation Electro-dialysis Reversal
Dr. Allen Alper: All that sounds very good. You could build equipment that's commercial size for producing large quantities of lithium concentrate?
Ben Sparrow: Certainly, we're a commercial company, two factories, hundreds of people. We just shipped a very large gold mine, brine treatment plant up to Canada's arctic for DFID industry gold mining. We were competing against some majors there, the biggest water companies in the world. In the case of this advanced lithium tech and membrane separation, it's a module. These are commercially produced today. The membranes are commercially produced. Treating larger flows just means more of those modules, more of those refrigerator sized cartridges.
Dr. Allen Alper: These units come as modules and depending on the volume, you would just add more modules, correct?
Ben Sparrow: That's exactly correct. They're commercially produced, but none have been used commercially in the lithium industry as yet. We've just started to see how this could add value to the lithium industry. There still needs to be a commercial demonstration. That's going to take an innovator, somebody with courage. Of course, people who do that will receive some benefits, if and when it's successful.
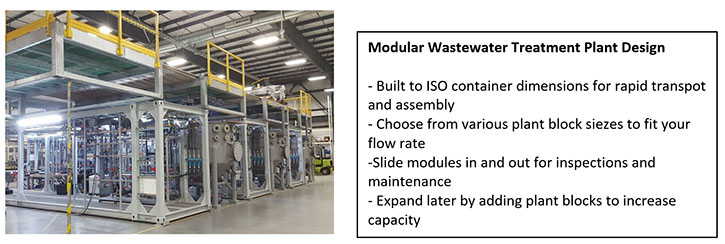
Ben Sparrow: We've been hired by Standard Lithium to help them develop and build their advanced pilot plant.
Dr. Allen Alper: That’s exciting! Excellent! You mentioned the gold application. Are there any other applications, with various mining companies, for which your technology might work?
Ben Sparrow: Sure. There are multiples. It's more of a conventional technology we practice, membrane systems to produce clean water for discharge into the environment, say from Tay labels or an evaporative system. Often companies will try and use a membrane system to its maximum capacity. Membranes have their limits. They can only concentrate so much, so if you imagine a pot of salt water on your stove, and you boil it down, if you keep boiling it down, eventually, you're going to get more concentrated and then you'll start making crystals, then you'll end up with a crust on the bottom of the pan. So, membrane systems can kind of deal with that top layer, they can concentrate it, sometimes reduce the volume by three to four times.
Then, once you get out of that realm, you're into thermal systems. You're into boiling water. So, we do both of those. We're really just starting to see the uptick in mining companies treating water for discharge. Historically, they haven't needed to. They've been able to store them in tailings and recycle the tailings, and we're seeing that uptick in two areas. One area is greenfield mines, our new mine development, and that was the gold mine plant that we just shipped today.
So, due to regulations, they can't either have tailings ponds, or have as large tailings ponds as they need to treat water. Another application is mine closures at end of life mines, where they need to treat all of the remaining water on site before they shut it down, but seeing very little activity in existing mines that continue to operate because they have their tailings impounded. Coal mines, metal mines, copper mines, gold mines, various types, particularly in the US are quite active. We're seeing a lot of interest in the retired mines.
Dr. Allen Alper: Very interesting, excellent! Could you tell us a little bit about your background and the team?
Ben Sparrow: The Management team, the Board of Directors, we're all highly technical. We're all either Ph.D. scientists or professional engineers. I'm a professional mechanical engineer. On the management team, we all received our MBAs roughly a decade ago, and were building various projects.
I was building large scale hydroelectric facilities, and specifically upgrading them, and rebuilding them, and re-powering them, so I come from a mechanical engineering/construction management/project management background. But in my free time, I was a hobbyist inventor, and I invented multiple processes that didn't work, and then I finally invented one that did work. A desalination system, and I built it in my apartment. I was probably evicted from the apartment because you're not supposed to build desalination machines in apartments. That was the start of the Company. I received my first patent and the technology was featured in The Economist.
Some oil and gas mining companies read about it. They came by and knocked on the door, specifically Teck Resources, and then Conoco, and Cenovus, and BP, and they all invested money. They said, "Hey, there's really something here!" That was a number of years ago. Since then, we've built up the company and are delivering these commercial products. We still invest heavily in R&D. Almost everything's plowed back into R&D and developing next generation technology because there is such a tremendous opportunity out there to develop new methods to treat waters that have not been treated before.
Humankind's just starting to get into that right now, where regulations are changing and improving in an effort to protect rivers and lakes, because a lot of the smart governments out there, like the United States, are definitely leaders in this. China's becoming a rapid leader, and so is India. They're recognizing that, if they want to have safe water for a millennia, the best way to do it is to protect the rivers and lakes. So, that's where Saltworks is focused. That's my background, including what I build by myself, others on the team have engineering, science and business backgrounds. Very, very technical!
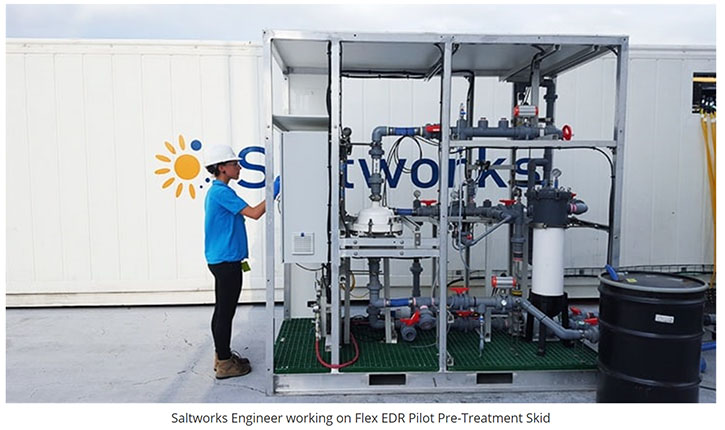 Figure 2 Saltworks Engineer Working on Flex EDR Pilot Pre-Treatment Skid
Dr. Allen Alper: That sounds very good. Could you tell us more about the Company’s ownership, the structure of the company and the investors?
Ben Sparrow: The Company’s privately held. The founders control the majority, the founders and employees, so we have vested shares for employees, and then we have these outside investors that I mentioned, British Petroleum, ConocoPhillips, Cenovus Energy, and Teck Resources. They invested because they saw the value of the technology and they want robust, reliable technology for their businesses, for their future, for beyond 2020, and those are exactly the problems on which we are working.
Dr. Allen Alper: Well, that sounds excellent! Could you tell our readers/investors why mining companies should consider using your services?
Ben Sparrow: First, if you don't need to treat the water, don't treat the water. Do everything you can to conserve, and to recycle. There are intelligent ways to recycle. For example, using our selective analysis system, you can just extract chlorides, and I'll give you a very specific example of that. Rather than treating tailings water, some companies may have tailings that are high in chlorides, which hurts either their process or corrodes their plant, and so, they'll want to treat it, discharge it, then remake with fresh. What you can actually do is you can selectively extract the chlorides.
We're doing a project in the US with a major cold power company. We're doing exactly that, we're just pulling out the chlorides. They've looked at all sorts of treatment, but in this instance it is better not to treat, but to remove the pollutants selectively, remove the trouble makers. So, step one is to conserve, step two is to see if you can recycle with some interesting processes, step three is to treat.
Companies talk to us versus others, because we are lower cost and high performance. Our customers are finding, due to the innovation, we're able to deliver a water plant that is higher performing, better automated, and ultimately, lower cost. There are big opportunities in the water treatment industry for our solutions because a lot of the automation has been quite rudimentary, almost shockingly so.
We build what we'd consider intelligent plants that clean themselves, diagnose themselves, take much greater care of themselves, which is particularly important for remote miners, and it reduces their workload. If anybody's considering a water plant, give us a shot. If they'd like competition versus the conventional water companies, we're happy to provide them that competition. If we don't win it, then, at least, we provided some competitive pressure to help those miners achieve their best price possible.
Dr. Allen Alper: Excellent!
Advanced Lithium Tech:
Animation of how monovalent selective electrodialysis reversal (mEDR) works:
https://www.saltworkstech.com/technology/flex-edr-advanced-electrodialysis-reversal-system/flex-edr-selective-ion-removal-system/
Spec sheet for mEDR (picture of stack on page 2):
https://cdn.saltworkstech.com/wp-content/uploads/2018/07/Flex-EDR-Specification-Sheet-1.pdf
Conventional Lithium Tech:
Chemical Softening;
https://cdn.saltworkstech.com/wp-content/uploads/2018/08/BrineRefine-Spec-Sheet-RH.pdf
Evaporative Crystallizers
https://www.saltworkstech.com/wp-content/uploads/2018/07/Saltmaker-MultiEffect-Spec-Sheet.pdf
https://www.saltworkstech.com/
Phone: +1-604-628-6508
North America Toll Free: +1-844-725-8688
info@saltworkstech.com
13800 Steveston Hwy
Richmond, BC, Canada
V6W 1A8
|
|