Sciaky Allows Fast and Efficient Production of Large-Scale, High-Value Metal Parts with its Revolutionary Electron Beam Additive Manufacturing (EBAM™) 3D Printing Technology
|
By Dr. Allen Alper, PhD Economic Geology and Petrology, Columbia University, NYC, USA
on 1/16/2017
Chicago-based Sciaky, Inc. has been a key supplier of advanced welding systems since 1939. Its groundbreaking Electron Beam Additive Manufacturing
(EBAM™) solution is a one-of-a-kind 3D printing technology that allows fast and efficient production of large-scale, high-value metal parts. Lockheed
Martin Space Systems is using a turnkey EBAM system from Sciaky to build titanium propellant tanks for satellites.
Dr. Allen Alper: This is Dr. Allen Alper, Editor-in-chief of Metals News, interviewing Jay Hollingsworth, public relations manager, Phillips
Service Industries. Tell us what your company does, and about its markets and products?
Jay Hollingsworth: I work for Phillips Service Industries, also known as PSI, which is the holding company of Sciaky, Inc. PSI is
located in Livonia, Michigan, which is a suburb of Detroit. Sciaky, Inc. is located in Chicago, Illinois. Sciaky has been around since 1939. Their
leading-edge welding technology was very critical for the production of Ally fighter planes back during World War II.
During the 20th Century, Sciaky’s biggest technology was manufacturing electron beam welding systems. Back in the late '90s, we started to
develop our additive manufacturing technology, which we initially marketed as Direct Manufacturing. As we began to fine-tune this technology, we
gained the attention of thought leaders in the aerospace and defense industries.
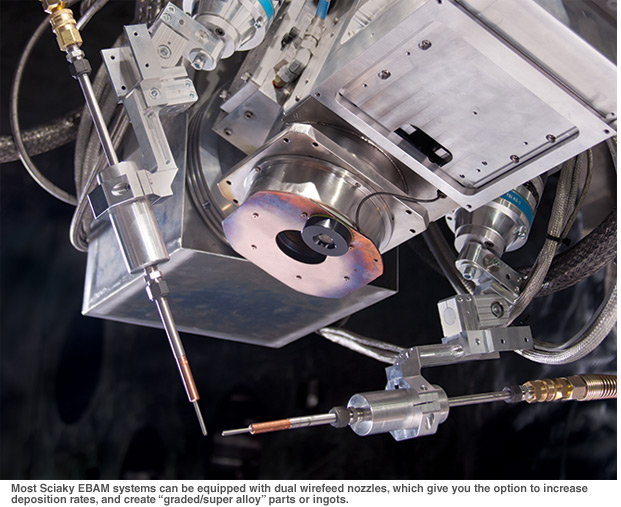
After more than a decade of high-level R&D projects and contract service work, Sciaky began to offer its Electron Beam Additive Manufacturing (EBAM™)
metal 3D printing systems for purchase to the commercial market in 2014. Within a few months, Lockheed Martin Space Systems purchased an EBAM system
to build titanium propellant tanks for satellites.
Dr. Allen Alper: How does Sciaky’s EBAM technology work?
Jay Hollingsworth: Starting with a 3D model from a CAD program, Sciaky’s electron beam (EB) gun deposits metal, via wire feedstock,
layer by layer, until the part reaches near-net shape and is ready for finish machining. EBAM systems can produce parts ranging from 8 inches (203
mm) to 19 feet (5.79 meters) in length. Gross deposition rates range from seven to 20 lbs. (3.18 to 9.07 kg) of metal per hour, depending upon the
selected material and part features. The best material candidates for EBAM include titanium, tantalum, Inconel, tungsten, niobium, and stainless
steels. Sciaky’s IRISS® (Interlayer Realtime Imaging & Sensing System), a patented Closed-Loop Control, makes everything possible. It provides
consistent part geometry, mechanical properties, microstructure, metal chemistry and more from the first part to the last.
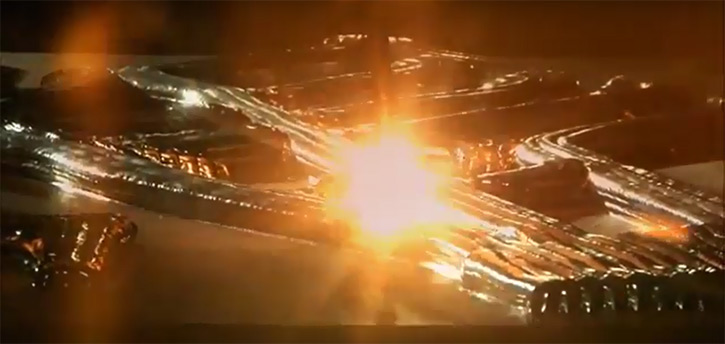
Dr. Allen Alper: John O'Hara, Global Sales Manager has joined us. What would you say the advantages of additive manufacturing are, John? What
generally leads most of the manufacturers to EBAM?
John O'Hara: The three big advantages of EBAM is the significant cost savings of material, the significant time and cost savings of post
processing, as well as the overall savings that is associated to producing a part 75% faster than traditional methods.
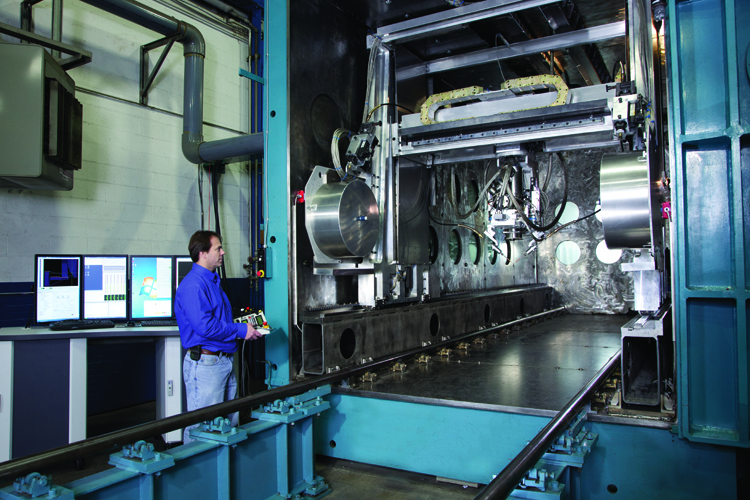
Some of the unique features of Sciaky's EBAM technology go beyond those three big advantages because the size of the parts that we make with EBAM are
measured in meters rather than centimeters. It would only make economic sense to make very large parts if you had a very high deposition rate. To
print metal measured in grams per hour is fantastic if your part only weighs what a pencil weighs. However, with parts that are going to weigh tens
or hundreds of pounds, that rate is not economically feasible. With EBAM’s industry-leading deposition rate, along with its large part format, we can
produce very large parts in a matter of hours or days.
A third and very important aspect that we think is unique in the market is our process control that we call IRISS. It is a suite of sensors,
software algorithms and other features that allows us to monitor the deposition process in real time and adjust to the inputs in order to get a
consistent result.
Dr. Allen Alper: How are you marketing Sciaky’s technology?
John O'Hara: We have been evolving our electron beam technology for 5 decades now, and we are starting to see manufacturers adopt 3D
printing technology worldwide. Sciaky has the expertise to help manufacturers become EBAM experts as well. Whether it is OEMs adopting EBAM as their
in-house manufacturing method, suppliers adopting EBAM to pass along cost savings to the OEMs, or educational institutions pushing the boundaries of
manufacturing technology, Sciaky is ready to support this new industrial revolution.
Dr. Allen Alper: That is exciting. What you have is like a pilot facility. If someone needs a certain part, they can come to you and you can
work up something. They can see it made and then order. Is that how it works?
John O'Hara: Essentially, yes. We frequently help customers who are at the entry-level stage by helping them understand the science of
EBAM, as well as helping them establish a business case for adopting EBAM. We have helped customers through the early stages of design, as well as
customers with low-level production requirements. Just recently, we assisted a European customer that only needed to produce eight to 10 parts a
year. At that level, it would be tough to justify them buying an EBAM system, but they are certainly benefiting from leveraging EBAM as a service
offering.
Dr. Allen Alper: Can you please elaborate a bit on the application for titanium airframe parts?
John O'Hara: Sure. There is a much wider use today of titanium in airframe structures for a few different reasons. Most of these
structures are critical to the function of the airplane. We call these flight-critical parts. Titanium is an excellent choice because of its
incredible strength-to-weight ratio. It is extremely strong and very lightweight, which helps save on fuel costs. We often see these titanium
airframe structures holding the wings on the plane and mounting the engine to the plane. Sometimes they are landing gear, doors, or very important
parts in the design of the plane. The drawback with titanium, of course, is that it is a very expensive metal, and it is very difficult to work into
its final shape. The post-process machining and heat treatment, along with other factors, make it very expensive. Today, these titanium airframe
structures are made with a forging process, which is a very expensive method of making metal parts.
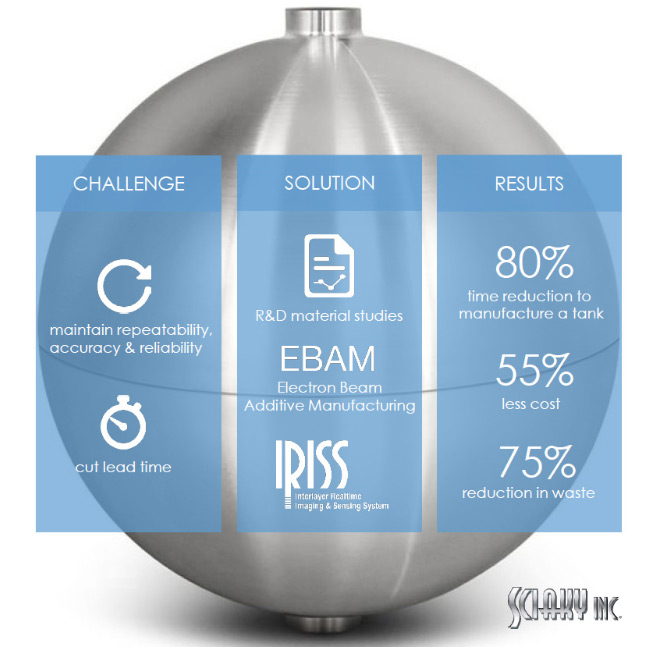
The good news is that additive manufacturing, or 3D printing, can replace some of the forging processes that take a long time to complete and are
very expensive. If we can print metal parts with the same material properties as forged parts, we can eliminate a lot of time, cost and waste from
the current forging process.
Dr. Allen Alper: How about your physical properties?
John O'Hara: The goal of the project that we are doing with Airbus, who recently purchased a Sciaky EBAM system, is to match the material
properties of the forged metal parts. The most recent data that we have indicates that we are meeting or exceeding forged metal part properties on
many tests.
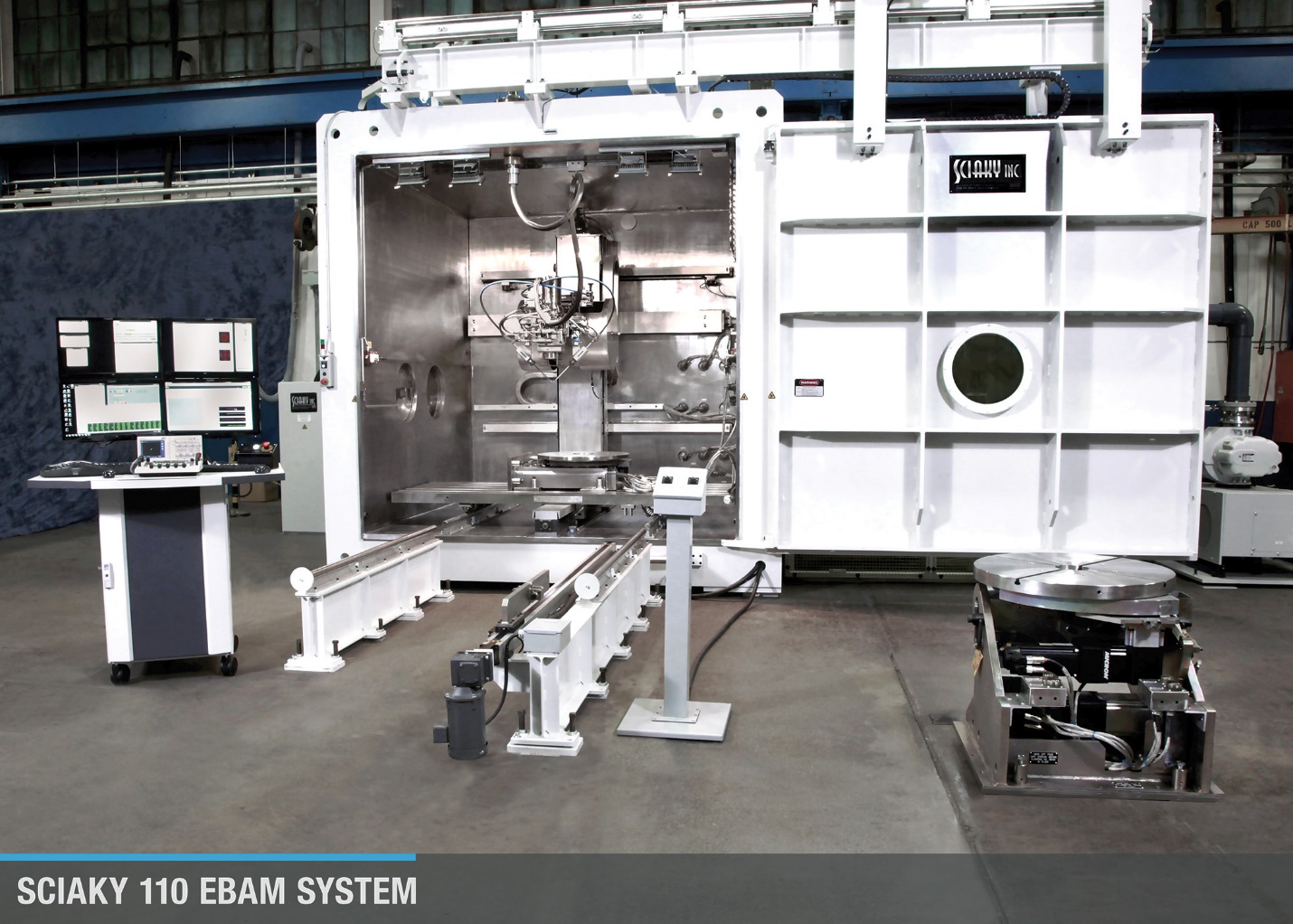
As our development goes forward, we will continue to refine the hardware in the machine, the software that we use to run it, the material input (the
wire feedstock we use), and the post processing, which includes the heat treatment and stress relieving that we do to the metal. All of these
different factors affect the properties. As we continue this project, we expect to meet or exceed the forged metal properties on all tests so that
EBAM becomes a drop-in solution for the forged metal parts.
We understand that EBAM is not going to replace forging. We are not putting the forging industry out of business. What we are aiming to do is
target the most difficult forged parts from the current forging method and introduce EBAM technology to help our customers significantly reduce time
and costs.
Dr. Allen Alper: That sounds very good, John. Is there anything else you would like to add about what your company is doing and what markets
you are serving?
John O'Hara: Absolutely. One distinction I would like to make is that we do not limit ourselves to just titanium. The more expensive the
metal is, the better the business case is for EBAM. There are nickel alloys and super alloys used in places like jet engines and power generation.
There are drilling and mining applications that we see frequently, even tool and die applications. We have an EBAM tool that is in production with a
major automotive manufacturer right now.
On the chemical processing side, we have some refractory alloys that are exceptionally corrosion resistant or high-temperature tolerant.
Things like Jay mentioned earlier – tungsten, niobium, tantalum – these are all metals that the traditional lasers and arc processors sometimes have
trouble even melting. The electron beam (EB) heat source that EBAM utilizes is really the enabler for high temperature metals.
Ultimately, we think EBAM is going to be a solution for any part made of a high value metal, regardless of industry.
Dr. Allen Alper: That sounds great. What would be an example of how much Sciaky’s EBAM systems cost?
John O'Hara: Cost can vary widely based on the size of the system and the features. However, customers can estimate somewhere between two
to six million (US Dollars). Obviously, the six million dollar system is a truly enormous machine that would meet very specific requirements, but it
does exist. We have designs for smaller machines, but again, they are not able to take advantage of the large part format. In fact, the smaller EBAM
systems tend to attract the research and development markets more than the production markets.
Our website, www.sciaky.com, has a list of all the available standard EBAM systems. They range from roughly a 2-meter cube up to 30 cubic
meters, something that I could drive my car through. Most customers find themselves in the 3-meter cube machine, which is better known as the EBAM
110. Of course, we always welcome the opportunity to quote machine costs, or service costs, based on a customer’s specific requirements. Sciaky is
available by phone at 877-450-2518. We are here to help every step of the way.
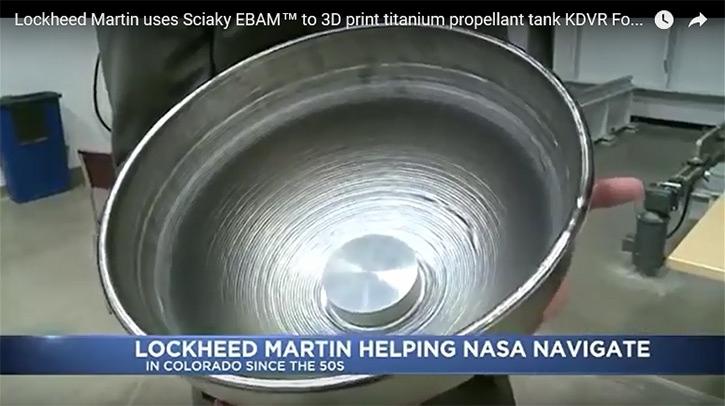
http://www.sciaky.com/
John O'Hara
Global Sales Manager
Mobile Tel: (312) 459-6849
Email: johara.sciaky@psi-corp.com
|
|